深度解读激光增材制造中的过程监控
技术基础
本文引用地址:http://www.amcfsurvey.com/article/201807/383695.htm激光增材制造(LAM)设备有两种类型:粉末床和送粉式。近期业内较多的关注集中在后者身上, 本文讨论的也主要是后者。
图1显示了通用的粉末床系统的原理示意图, 在该系统的整个工作区中使用刮板来进行平整粉末的步骤, 以在构建平台上建立粉末床, 整个过程是在可以控制内部环境的成形保护室内进行。激光能量传递到粉末床的表面,引起粉末的局部熔化和融合,使得该区域的金属粉末固化。
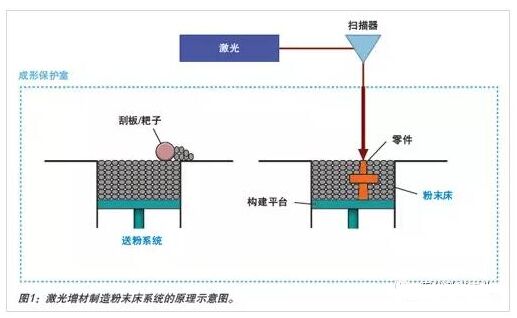
通常情况下,每一道激光扫描能熔化并重新凝固数层粉末,粉末层的厚度通常为20至150μm。在每一次激光照射后将额外的粉末从工作区刮掉,然后重复上述过程,直到构建出一个坚固的三维(3D)零件。每一个“构建”过程包含数以千计的分层,因此每次运行需要花费几十到几百个小时。每一次“构建”可以生成数十个相同或不同的零件。
由于在金属增材制造过程中是一层接着一层熔化并且快速凝固,所以零件经历了涉及定向热传递的复杂的热演化历程。一些主要用于航空航天和医疗/牙科应用的合金零件甚至可能会遇到反复的固态相变。这些因素使得对成品显微结构属性的分析,相对那些使用传统方式制造的零件而言,变得更为复杂。频繁的定向热量提取会导致晶粒结构在Z轴方向(垂直于构建平台)呈柱状,并且“在增材制造中,各处的显微结构和力学性能通常呈各向异性,而Z轴方向一般是最弱的”。激光选区熔化(SLM)工艺的典型缺陷包括显微疏松以及相邻层之间融合不好。航天应用特别关注的是靠近零件表面的孔隙引发的疲劳裂纹,同时表面光洁度也会对疲劳寿命造成影响。
综合上述问题一起考虑,特别是那些对结构起到关键作用的零件,广泛应用增材制造技术所要面临的重大挑战是成品的合格性以及如何检定其合格性。最近,关于增材制造的一些报道都在呼吁借助在线、闭环的过程控制和传感器来确保增材制造的质量、一致性和再现性。总体的目标是在空间分辨率低于1mm2的情况下实现稳定的分层质量评估,这将免除通常在构建后进行的检测或破坏性测试。领先的航空航天制造商也非常支持在线监测:GE航空发动机公司的增材制造业务拓展总监Greg Morris先生说:“如今,增材制造一个引擎零件所需要的时间中有25%是用于后检测工序。通过在构建过程中实时进行在线检测,我们将加快增材制造引擎零件的生产速度,例如LEAP燃油喷嘴。”
设备和工艺的多变性
过程监控解决的主要问题是增材制造设备或激光与材料的相互作用所具有的多变性,因为后者会反过来扰乱金属的微观结构或宏观力学性能。包括构建平台和成形保护室的温度、保护室的氧气浓度、惰性气体流经粉末表面的速度在内的环境因素将会影响工艺转换和缺陷的形成。在每一次激光扫描过程中,激光功率、焦斑大小和z轴方向的功率密度变化是决定材料热偏差的潜在波动的关键参数。晶粒的粒径分布和形状将会影响每一层粉末结合的状态,从而影响激光增材制造零件的表面质量和密度。关键的运行参数包括扫描速度和扫描间距(x-y),尽管如今的振镜扫描器在这些方面表现得足够稳定,并且再现性很好。每一个分层的构建或者说“重涂覆”过程也必须在层厚的均匀性以及每层的可重复性方面保持高度一致。最后一点,零件的几何形状将会影响热传递过程。材料的悬垂部分和尖锐棱角部位的热传递有所不同,会引起应力变形以及孔隙、针孔或显微裂纹。SLM Solutions NA公司北美地区运营副总裁Jim Fendrick指出:“局部的热力状态决定了整个过程,几何形状也有关系。”
如何保证质量
鉴于影响材料累积热暴露的参数非常多,增材制造设备实现实时质量保证(QA)的方法分成三类:
◆ 传感器监控和控制设备状态的各个方面;
◆ 粉末床表面或层厚的缺陷/不规则的评估技术;
◆ 对激光与材料的小的相互作用区或者说“熔池”的直接传感。
领先的增材制造系统供应商,例如SLM Solutions(德国Lübeck)公司、Concept Laser公司和EOS公司(德国Krailling),都在借助模块化硬件和软件的方法来应对这些挑战。EOS为其模块命名为“EOSTATE”,而Concept Laser则将其命名为“QM”(质量管理)模块。SLM Solutions公司的最新系统最多能包含六大模块,每一个模块都是根据自身的功能来命名。
设备状态的传感
这是商业化增材制造设备实现其“过程监控”的第一个方面。第一步是控制成形保护室内部的状态。对惰性环境的温度和残余氧气含量、构建平台的温度和系统的气体净化过滤器的压差进行监控、管理并录入计算机。Concept Laser的QMatmosphere模块能调节成形保护室的氧气浓度,而EOS的EOSTATEBase模块能同时监测几个成形保护室和其他的设备状态。SLM Solutions的Sensors模块能监测整个设备范围内数个位置的温度、过滤器的状态、成形保护室内的氧气浓度,并且每隔两秒就将这些数据录入到计算机。
设备状态传感的下一步涉及到激光器和光学元件。截至撰写本文为止,激光器/ 光学元件的监测通常包括简单地将激光子系统和扫描器自校准的额定状态的数据录入计算机(EOS的EOSTATE Base)、测量和控制激光功率(EOS的EOSTATE LaserMeasurement模块、Concept Laser的QMlaser模块和SLMSolutions的Laser Power模块)。
因为激光的功率密度决定着熔池的大小以及激光光束经过粉末时引起的温度变化,所以对激光光束的束腰定位或相对于粉末表面的焦散面进行控制也是非常重要的。SLM Solutions公司的Caustic Control模块可以实现上述功能。
收集轴上光发射并分离到传感器中,从而对焦斑大小、焦平面位置和光束能量分布进行连续检测。当发生焦点漂移或者情况发生变化时,警报将被触发,或者构建过程将被终止。
增材制造设备供应商也已经开始监测和控制粉末床的均匀性。这通常需要获取整个粉末床的可见光图像,在图像中,那些非均匀的部分将会被比对出来。EOS最新设备的EOSTATE PowderBed模块包含这一功能,可以把每一层的两幅图像记录下来以备线下检查。同样,SLM Solutions公司的Layer Control System模块能在每一次粉末重涂覆和每一次激光照射后抓取分层表面的图像。在构建过程中对图像进行自动分析和异常检测,并标记出来。当构建多个相同的零件时,对图像子区域进行局部分析,可以显示出每个零件在构建过程中的误差。这样就可以停止构建有缺陷的零件,同时继续构建其他没有缺陷的零件,从而节省时间和材料。
评论