基于现场总线控制技术的转炉煤气回收自控系统
1 引言
本文引用地址:http://www.amcfsurvey.com/article/201609/303359.htm莱钢炼钢厂1#~3#转炉煤气回收自控系统于98年12月投产。该自控系统承担着将三座转炉吹炼时产生的大量的转炉煤气净化、合理化分析后进而加以回收再 利用的自动化控制任务。
但随着投运时间的推移,该系统暴露出的问题越来越突出:控制硬件/软件老化、过时--plc为西门子s5-135u,工控机为老式的奔腾166 机型,编程 软件、监控软件分别为基于dos的step5和fix;控制方式落后--plc与现场信号的连接均采用传统的硬线连接方式,通讯网络为sinec-h1 网,详见图1;系统的故障率逐年上升,严重制约着生产的顺行。因此,对该控制系统进行全面的更新,以使其能够迅速满足生产的需求变得十分必要。莱钢自动化部技术人员经过认真研究、分析、论证,采用了目前流行的现场总线控制技术对其进行改造。
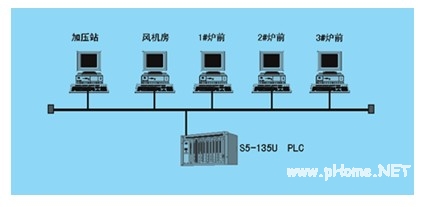
2 现场总线综述
现场总线是连接控制系统中现场装置的双向数字通讯网络,它与传统的控制方法相比,具有十分明显的优势:
(1) 具有很好的性价比,可大幅度降低系统的综合成本;
(2) 采用了数字通讯技术,有效的提高了系统的测量及控制精度;
(3) 数据传输更为可靠、系统响应更为快速,同时还具有强大的抗干扰能力;
(4) 具有故障自诊断、短路自保护等功能,极大的方便了系统的维护,提高了系统的安全可靠性。
3系统设计
3.1 控制网络
基于现场总线与传统的控制方法相比具有无法比拟的优势,控制方式采用现场总线技术。同时,转炉煤气回收现场控制设备的分散性以及恶劣的现场环境也十分适合 采用现场总线控制技术。
目前流行的现场总线协议有多种:profibus-dp、profibus-pa、devicenet、canopen、modbus等,各种现场总线协 议都具有各自的特点和优势。结合转炉煤气回收特点,为了获得更好的响应、可靠性和更高的效率,主plc与远程i/o采用了具有世界标准的 profibus-dp现场总线通讯方式。profibus-dp是目前最快的开放式标准总线,使用基于rs485标准的物理层,并采用主-从工作方式; 其网络通讯距离长(最长可达10公里),通讯速率高(最高达12mbps),具有极好的抗干扰性能,快速的i/o采集特性(1000点的扫描时 间1ms)以及超大容纳量(最多126个节点、几千个i/o点)。
plc与上位机则采用了基于tcp/ip协议、星型拓扑结构的以太网通讯方式。该通讯协议更为普遍、通用,同时具有很高的通讯速率;星型连接的拓扑结构使 得网络的可靠性、扩充性更强;由于网络走线距离长,通讯介质采用光缆,可以最高支持100mbps的通讯速率、几十公里超长的传输距离、很强的抗干扰能力 以及极低的误码率,而且投资成本低、施工简单、维护方便。
3.2 控制硬件
根据控制系统的规模,采用西门子s7-300 plc进行控制。siemens s7系列plc具有更为强大的功能,更快的扫描速度,可以完成更为复杂的控制,同时还支持多种通讯协议,兼容性好,具有更为出色的电磁兼容性,可以满足各种工业标准。
为了能够适应恶劣的工业环境,我们采用了turck功能最为强大、等级最高的pdp、sdpb系列i/o模块作为远程站进行现场设备的信号采集及控制。 turck输入/输出模块防护等级远远高于普通的plc i/o模板(ip20),可达ip67,非常适合安装于极其恶劣的现场中,同时还具有强大的自诊断功能,能够迅速准确的发现节点、电源、现场信号等故障,并具有短路诊断/保护功能以及组、点诊断及保护功能,便于系统维护。另外,采用了3套turck公司的bl20产品放置于电磁站内,分别用于3座转炉的炉 前控制。bl20产品支持多种总线协议,具有非常好的开放性,同时i/o点数配备灵活(每块模板从1点至32点不等,提供多种选择),安装体积小,特别适 合于小型精确项目(每座转炉炉前控制信号di只有9点、do为6点)的开发,降低投资费用。
此外,由于该系统的控制节点较多(共42个),已经超过了profibus-dp网络每段所能容纳的最大节点数32。为此,配置了中继器将系统的容量提高 了1倍,同时更为有效的提高了网络的通讯速率,使网络的负载量分配更为合理。
3.3 控制软件
plc编程软件/监控软件分别采用基于windows 2000平台的step7 5.1+sp2及wincc v5.1,用于编制控制程序和监控画面。原系统中采用step5开发的控制程序可以通过step7软件自动转换为s7 plc程序,再根据改造情况进行适当的修改后即可投运,从而大大缩短软件开发周期。
4 系统配置与结构
plc i/o模板主要完成就近的4台风机变频器的相关信号控制;cpu采用现场总线通讯协议完成与现场远程站的数据传输;cp则负责与上位机的数据交换。
(1) plc具体配置为:
支持profibus-dp总线协议的cpu 315-2 dp 1块、支持tcp/ip通讯协议的cp 343-1 1块、ps 307(考虑到主机架模块的背板电流消耗较小,电源模块容量选择为5a) 1块、32点24v di模板3块、32点24v do模板2块。
(2) 炉前控制采用bl20,pdp、sdpb系列i/o模块则用于现场控制。
硬件具体配置:
l 现场控制
4 路ai模块(sdpb-40a-0007)21块、4路rtd模块(sdpb-40a-0009)11块、16点di(pdp-im16-0002)3 块、8点do(pdp-om8-0004,2a)4块。
l 炉前控制
3座转炉炉前控制系统的硬件配置相同,均为 profibus-dp耦合器(bl20-gw-pbdp-12mb,12mbps)1块、总线电源模块(bl20-br-24vdc-d)1块、32点 di模板(bl20-32di-24vdc-p)1块、输出模板供电模块(bl20-pf-24vdc-d)1块、16点do模板(bl20-16do- 24vdc-0.5a-p,0.5a)1块。
l 上位机则全部采用高性能的台湾研华工控机ipc-610h(p2.0/256m/40g)。
系统配置图如图2所示。
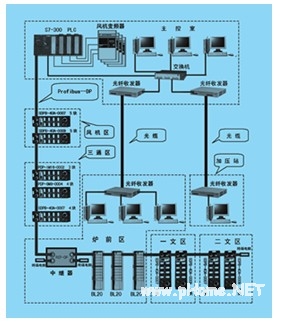
5 生产工艺简介
转炉吹炼生产过程开始后,风机由低速变为高速运转,氧枪下降开始吹氧,分析仪投入运行,经过一段时间后,烟罩降下。经过短暂延时后,炉口微差压开始自动调 节。当回收煤气的条件满足后,水封逆止阀自动打开,三通切换阀则由放散侧转换至回收侧开始回收煤气。停止吹炼前烟罩首先被升起,炉口微差压调节系统停止调节,二文喉口rd阀置于固定位置。在吹炼结束时,风机降为低速运转,二文喉口捅针开始动作,动作数次后,一次回收过程结束。若回收煤气过程中条件不满足,三通切换阀将自动由回收状态切换至放散位,水封逆止阀也自动关闭。该回收自控系统在转炉的每次冶炼周期只进行一次回收。为了确保安全,如果一旦进行放散, 即使回收条件再次满足,本冶炼周期内也不再进行回收。
评论