高精度电池测量为电池管理增添了实际价值
目前这一代电动汽车依靠能量范围介于 16kWh 至 53kWh 之间的锂离子电池组提供动力。而仅仅一加仑汽油所包含的能量就超过了 36kWh。对于电动汽车或混合动力汽车 (HEV) 抑或是任何的大功率电池系统来说,若要与内燃机 (ICE) 展开竞争就必需充分利用电池的全部储能。为此,必须对电池组内部的每节电池进行仔细周密的监视和控制。
本文引用地址:http://www.amcfsurvey.com/article/174732.htm大功率电池组由一长串串接电池组成。电池监视器 IC 直接连接至每节电池,负责准确地测量每节电池的电压。这绝不是一件简单的工作,因为各个电池位于一个非常高电压电池串的不同点上,而电池串很容易遭受惊人的电尖峰和电磁干扰 (EMI)。电池管理系统 (BMS) 整合了电池电压与电流、温度和工作情况记录,以连续获知每节电池的状况。虽然这是一项棘手的难题,但利用准确的监视和控制仍可实现电池组行车里程、可靠性和安全性的最大化。
HEV 或 EV 中电池的预计使用期限是 10~15 年,而当电池失去其原始容量的 80% 时即被认为处于其寿命末期。通过限制工作电荷状态 (不允许电池满充电或完全放电),可最大限度地增加电池的使用寿命和可靠性。典型的电池组工作于一个受限的范围内,例如:20% SOC 至 80% SOC,其中 SOC 表示“电荷状态”。这些 SOC 限值可根据电池的老化和工作情况 (比如:高温环境) 进行调节。由于采用了此类限值,故电池组不会以满容量地使用。例如:以 20% SOC 至 80% SOC 来运作电池组将把可用 SOC 限制在这 60% 范围。BMS 所面临的挑战是使每节电池尽可能接近限值运作,而不要超过限值。锂电池在其工作范围内表现出平坦的放电曲线,使得上述挑战的难度进一步加大。因此,在整个工作范围内电池电压的变化非常之小,作为 SOC 计算的一部分,电池监视器必须进行非常准确的测量。
为了阐明电池测量准确度的重要性,我们来看一下简化的锂电池放电曲线 (示于图 1)。该曲线在整个工作区内具有一个恒定的 5mV/% (SOC) 斜率。倘若电池电压测量准确度欠佳,那么工作在 20% 至 80% SOC 范围之内且具有相似放电特性的电池组将面临严重的不利后果。
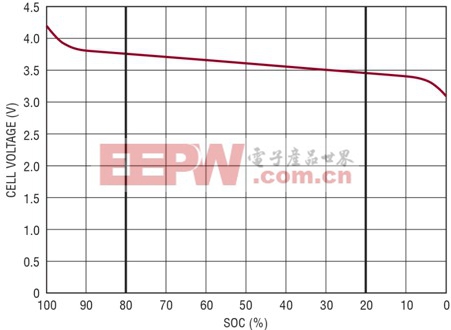
图 1:简化的电池放电曲线
如图 2 所示,倘若电池监视器具有一个 ±10mV 的电池电压测量误差,则 3.75V 的电池电压测量值实际上有可能对应的真实电池电压介于 3.74V 和 3.76V 之间。这对应的实际 SOC 范围为 76% 至 80%。由于存在该测量误差,因此必须利用一个“保护带” 对工作范围加以限制,从而确保不超过工作限值。在本例中,必须把工作范围限制在 22% 至 78% 的测量范围 (而不是 20% 至 80%)。假如期望电池组保持相同的范围,那么具有该准确度的 BMS 将需要额外的电池容量以补偿保护带限制。假设 60% 的可用 SOC,则电池容量必须加大 7% (注 1) 以补偿 ±10mV 的电池测量误差。对于一辆使用价格 3000 美元的 5kWh 电池组 (即每 kWh 电能的成本为 600 美元) 的 HEV 来说,这将造成成本额外增加 214 美元。
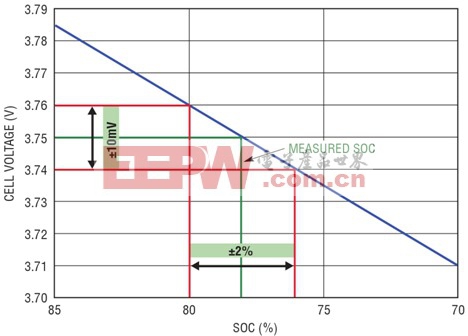
图 2:针对 ±10mV 电池测量误差的保护带要求
可以扩展该论点以凸显针对各种不同电池测量误差的“保护带损失”及其与 SOC 范围的相关性。如图 3 所示,测量误差仅为 1mV 的系统所需的额外电池容量不到 1%,甚至当电池组被限制在一个 25% 至 75% 的 SOC 范围 (即 50% 的可用 SOC) 时也不例外。
评论