基于MCU的离线锂电池充电器设计
高效、低成本及可靠的电池充电器设计可用各种方法来实现,但采用8位闪速MCU不仅能缩短设计时间、降低成本及提供安全可靠的产品,而且还能使设计人员以最少的工作量来进行现场升级。
图1:(a):降压转换器开关“开”;(b):降压转换器开关“关”
考虑到电池安全充电的成本、设计效率及重要性,基于MCU的解决方案可为设计者们提供诸多优势。通过选择带适当外围与闪存的8位MCU,工程师们能充分利用其优势来设计一种离线锂电池充电器。带2KB闪存及适当外围以提供一种廉价解决方案的飞利浦 80C51型MCU就是这样一个例子。集成化闪存还能提供高效及方便地调试应用代码并进行现场软件升级(如果需要)的能力。
由于设计界不仅熟悉而且广泛接受8位MCU,故软硬件开发可快速进行。由众多厂商提供的各种功能强大且并不昂贵的应用开发工具,也是这种方法的另一项优势。
利用这种方法,设计团队不仅能极大地缩短设计周期,而且还能进行更为复杂的设计,并使项目的整体材料费(BOM)不超出可接受的范围。
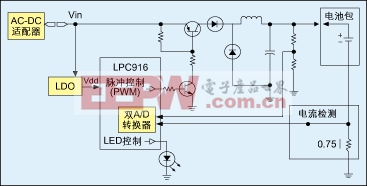
外围电路集成
譬如,当MCU集成有内部振荡器时,离线锂电池充电器设计可从以下两方面获益。首先,可省掉外部振荡器,从而节省成本及PCB占位;其次,内部振荡器可提高系统启动时的稳定性。
四通道A/D转换器是设计工程师们应该寻求集成到芯片中的另一种有价值的外围电路。除能比使用外部A/D转换器更节约成本外,还能用它来检测充电电压、电流及电池温度--几乎包括安全电池充电操作中的所有重要参数。
用来实现以下所介绍设计的MCU(P89LPC916)不仅集成了上述所有这些特性而且还拥有可同时在两个时钟上执行指令的高性能处理器架构,从而将其性能提高至标准80C51器件的6倍。Time0(计时器0)很容易被配置成PWM输出,故易于设置及使用PWM功能。
基本电池充电标准
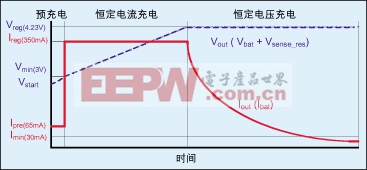
图3:锂电池充电过程
本设计为专门针对额定700-750mAh、3.6V放电电压及4.2V电压极限的锂电池充电器解决方案。
充电顺序分成以下三个阶段:预充电阶段、恒定电流充电阶段及恒定电压充电阶段。
当电池只剩下很少的电量且因此而只能产生很低的输出电压时,就必须有预充电阶段。在此情况下,必须采用低电流充电以保护电池。但如果被充电电池可产生较高电压(>3V),则可省略掉预充电阶段。当然,这是最普遍的情况。
大部分电能是在恒定电流及恒定电压充电阶段从充电器流入电池。电池的最大允许充电电流由该电池的额定容量决定。对于快速充电,例如额定700mAh的电池,可用350-400mA电流来充电。
在锂电池情况下,MCU必须在保持电池正常充电电压的同时还监视充电电流,以在电池充满时能终止充电过程。
温度监视可用来确保执行安全的充电步骤,因为随着电池充满,任何额外的电能都将被转换成热量。尽管MCU必须为其完成的功能增加温度监视,但当今市场上的大多数锂电池都带有内置过充电保护,故温度监视尽管需要但却很少使用。
降压转换器设计
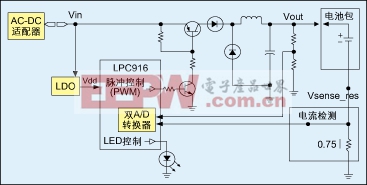
图4:测试电路
若要设计一种带锥形端接特性的充电器,最有效及最经济的方法是采用降压转换器来作为开关调整器。降压转换器使用电感来储存电能。图1a及1b分别为开关处于通/断位置时的降压转换器工作示意图。
来自PWM的信号控制充电开关。当开关闭合时(图1a),电流由于充电器提供的电压(充电器Vin)而流过电路,此时电容通过电感充电。
当开关打开时(如1b所示),电感试图通过感应电压来保持电流流动,但它不能立刻充电。然后电流流过肖特基二极管并给电容充电。此过程循环往复。
当通过减少PWM占空比来缩短开关“通”时间时,平均电压减少。相反,当通过增加PWM占空比来延长开关“断”时间时,平均电压增加。故通过控制PWM占空比来使MCU调整充电电压(或电流)可达到所需的输出值。
在讨论设计细节以前,需先讨论与电感及电容有关的两个要点:
1.电感大小
不难看出,确定降压转换器电感的大小是达到合适充电电压及电流的关键。电感大小也与成本有关。电感容量可用公式1来计算:
公式1
红外热像仪相关文章:红外热像仪原理
评论